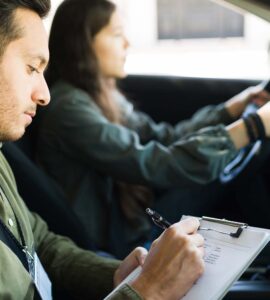
How Exactly Does a Liquid Filling Machine Work?
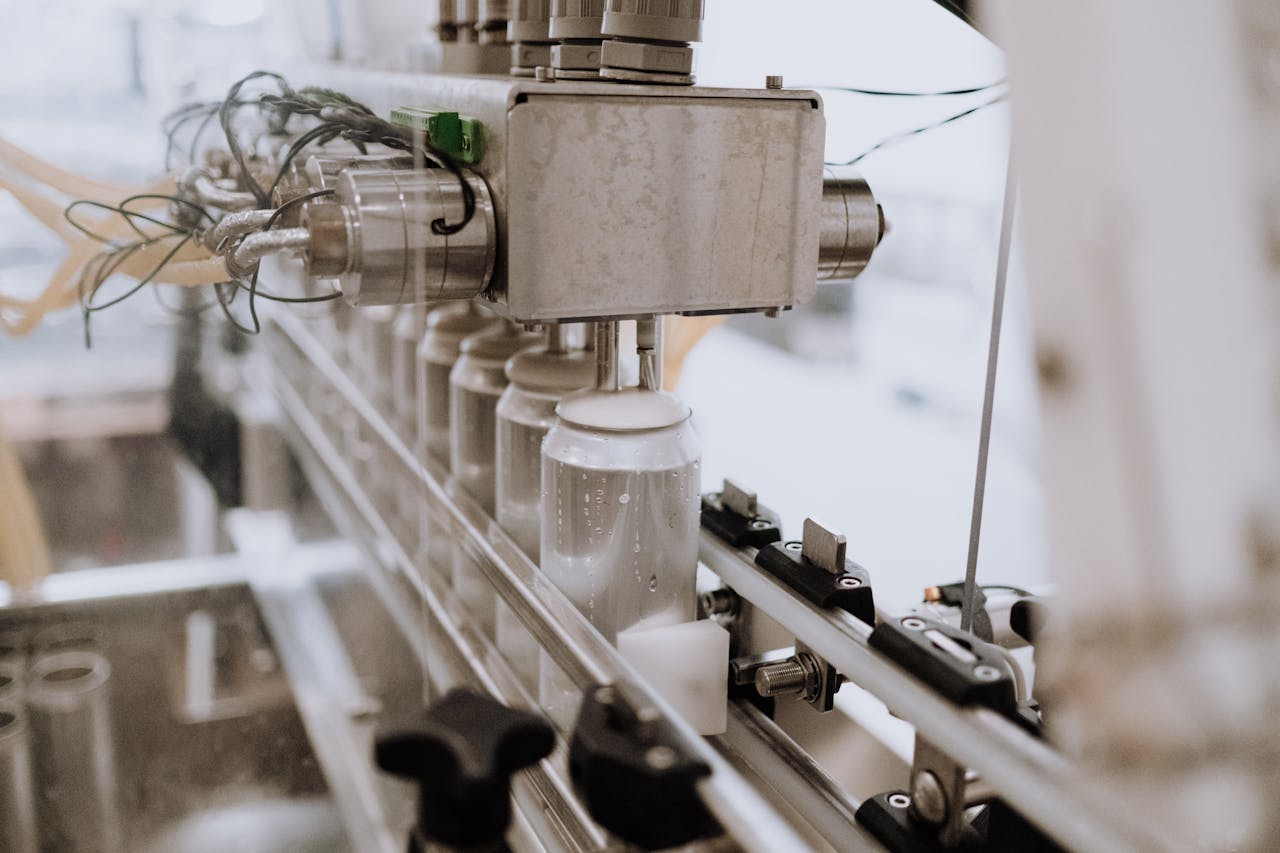
In the world of manufacturing and packaging, efficiency and precision are paramount. Liquid filling machines play a crucial role in various industries, including food and beverage, pharmaceuticals, cosmetics, and chemicals. But how exactly does a liquid filling machine work? This blog post delves into the mechanics and functions of these essential devices, exploring the different types and their applications.
The Basics of Liquid Filling Machines
A liquid filling machine is designed to accurately dispense liquid products into containers, ensuring consistency and reducing waste. These machines are essential for maintaining product quality and meeting production demands. They can handle a wide range of liquids, from thin, water-like substances to thick, viscous materials like syrups and creams.
Types of Liquid Filling Machines
There are several types of liquid filling machines, each suited to different types of liquids and production needs:
- Gravity Fillers: Ideal for thin, free-flowing liquids, gravity fillers use the natural force of gravity to fill containers. The liquid is stored in a hopper above the filling nozzles, and gravity helps it flow into the containers below.
- Piston Fillers: These are versatile machines that can handle both thin and thick liquids. A piston filler uses a piston to draw liquid from the supply tank and then dispense it into containers with precise volume control.
- Pump Fillers: Pump fillers use different types of pumps (gear pumps, peristaltic pumps, etc.) to move the liquid from the supply tank to the filling nozzles. They are ideal for handling high-viscosity liquids and ensuring accurate fills.
- Overflow Fillers: Designed for products where a consistent fill level is crucial, such as beverages in transparent bottles. Overflow fillers ensure that each container is filled to the same level, regardless of slight variations in container volume.
- Vacuum Fillers: Often used for filling glass bottles with non-carbonated liquids, vacuum fillers create a vacuum to draw the liquid into the container. This method is particularly useful for maintaining the integrity of delicate products.
The Working Principle of Liquid Filling Machines
The basic working principle of a liquid filling machine involves several key steps:
1. Preparation
Before the filling process begins, the machine is set up according to the specific requirements of the product and containers. This setup includes adjusting the fill volume, nozzle positions, and conveyor speed.
2. Container Positioning
Containers are fed onto the conveyor belt, which moves them into position under the filling nozzles. Sensors and indexing mechanisms ensure that each container is correctly aligned for filling.
3. Filling Process
- Gravity Fillers: The filling nozzles open, allowing the liquid to flow from the hopper into the containers below. The flow is controlled by gravity and shut-off valves to ensure accurate filling.
- Piston Fillers: The piston draws liquid from the supply tank into a cylinder. Once the cylinder is filled, the piston pushes the liquid out through the filling nozzle into the container. The volume of liquid dispensed is controlled by the piston’s stroke length.
- Pump Fillers: The pump draws liquid from the supply tank and pushes it through the filling nozzles into the containers. The amount of liquid dispensed is controlled by the pump’s speed and duration.
- Overflow Fillers: Liquid is pumped into the containers until it reaches a predetermined level. Excess liquid overflows back into the supply tank, ensuring consistent fill levels.
- Vacuum Fillers: The filling nozzle creates a vacuum inside the container, drawing the liquid in. Once the desired fill level is reached, the vacuum is released, stopping the flow of liquid.
4. Sealing and Capping
After filling, the containers move to the next stage of the production line, where they are sealed or capped. This process ensures that the product is protected and ready for distribution.
5. Quality Control
Quality control mechanisms are in place to check for fill accuracy and consistency. Any containers that do not meet the specified criteria are rejected and removed from the production line.
Advantages of Using Liquid Filling Machines
- Precision and Consistency: Liquid filling machines ensure that each container is filled with the exact amount of liquid, reducing waste and ensuring product quality.
- Speed and Efficiency: These machines can fill hundreds or even thousands of containers per hour, significantly increasing production rates.
- Versatility: With different types of filling machines available, manufacturers can handle a wide range of liquids and container types.
- Hygiene and Safety: Automated filling reduces the risk of contamination, ensuring that products meet hygiene and safety standards.
Conclusion
Liquid filling machines are an integral part of modern manufacturing, providing the precision, speed, and efficiency needed to meet today’s production demands. Understanding how these machines work helps appreciate the complexity and innovation behind the seemingly simple task of filling containers with liquid. Whether it’s a gravity filler for thin liquids or a piston filler for thick creams, each type of liquid filling machine plays a vital role in delivering consistent, high-quality products to consumers.